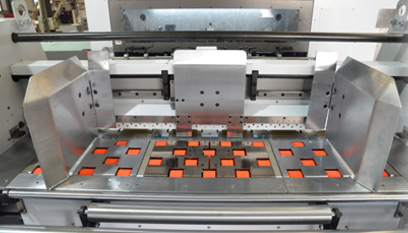
Lead Edge Paper Feeding unit
1.The lead edge paper feeding device adopts a non-stop downward suction paper feeding method, which overcomes the warping of cardboard caused by differences in temperature, humidity, surface paper gram weight, etc., making the paper feeding smooth and stable.
2,The lead edge paper feeding device adopts a dual-servo independent motion control system, suitable for all kinds of color-mounted corrugated cardboard; the transmission mechanism uses the combination of cams and gears, and the movement is stable and reliable;
3. The paper feeding wheel is designed with a widened width, with large friction and not easy to crush the paper. The lifting plate mechanism adopts finely ground mirror electroplating, and is not easy to scratch the surface of printed matter.
4. Both the side paper stopper and the front paper stopper are electrically adjusted, saving time and convenience.
5. The frequency conversion controls the suction air volume of the fan, and is suitable for paper feeding requirements of different thicknesses from F to seven layers (not more than 12mm).
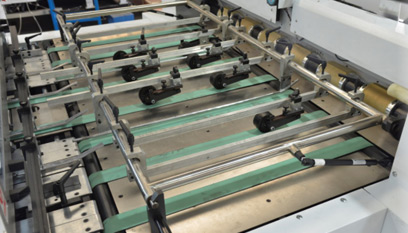
Paper Positioning and Conveying Section
1. The paper feeding and conveying adopt servo independent drive, and the motion trajectory is designed with a sine curve to ensure accurate paper positioning.
2. The paper feeding step distance can be adjusted without stopping the machine, enabling fine adjustment at any time.
3. The side lay adopts a large stroke design, which reduces the requirements for paper stacking and alleviates the operation intensity of the operator; at the same time, it is equipped with a non - stop fine tuning function, improving the working efficiency of the equipment.
4. The split - type front lay design is not likely to cause the problem of the face paper chasing and colliding.
5. The fine adjustment pressing type paper supporting mechanism cooperates with the front lay paper feeding mechanism, which not only ensures the smooth conveyance of warped paper but also improves the die cutting accuracy.
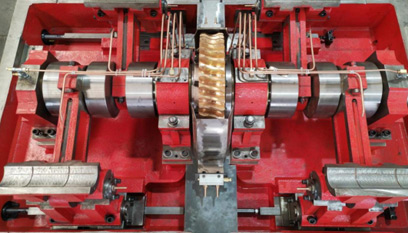
Main Transmission Part
1. The main transmission adopts a worm - gear and crank - connecting rod mechanism, featuring low noise, high pressure, high precision and long service life. The worm gear, swing rod and bearing bush are all assembled through manual scraping and lapping, with smooth meshing.
2. The base of the main machine and the upper and lower die - cutting platforms are all made of high - grade ductile iron materials and have undergone aging treatment. They are characterized by wear resistance and low deformation coefficient.
3. The crankshaft and the swing rod shaft both adopt a weighted symmetrical design, with uniform and stable force.
4. The lubricating oil circuit adopts a forced oil supply system, with good heat dissipation and sufficient lubrication.
5. A pneumatic clutch is adopted, with fast reaction speed, and accurate and stable actions such as starting, emergency stop and inching, and is maintenance - free.
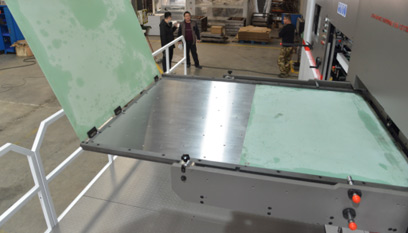
Paper Die - cutting Department
1. The die - cutting plate is installed in a four claw nut fastening manner, ensuring that the large format die cutting plate is always flat all the time, and is equipped with a pneumatic plate locking device, effectively reducing the plate changing preparation time.
2. The die - cutting steel plate is made of 7mm quenched manganese alloy steel material, with a long service life. It is equipped with a steel plate air floating device, making it convenient and labor - saving to load and unload the steel plate.
1
3. The fixed backing plate of the die - cutting plate frame is made of 5 mm manganese steel plate, which is not easy to deform and bend; the split - type epoxy resin backing plate saves time and effort in patching the plate.
1
4. The 320 type intermittent mechanism is adopted, and the 215° stroke angle has a stable transmission, reducing paper connection points and being not easy to loose the plate.
1
5. Background suppression dual photocell detection is configured at both the paper inlet and the paper outlet, and both dark and black papers can be detected.
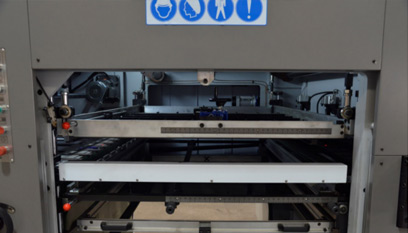
Stripping Department
1. The upper, middle and lower frames all adopt the center positioning system for plate - alignment, which is convenient for adjustment.
2. The upper frame is controlled by the motor together with the worm - gear self - locking reducer, ensuring that the upper frame will not fall off after being lifted; at the same time, it is convenient for inching to adjust the strpping needles.
3. For papaer stripping of the lower frame, the drawer - type is adopted, so that the stipping tools can be quickly loaded, unloaded and adjusted; at the same time, it is convenient for removing waste from small holes and laminated papers.
4. The transmissions of the upper, middle and lower frames all adopt cam connecting rod transmissions without chains and are maintenance free; at the same time, all three frames use steel sliders with wear - resistant copper bushings embedded, so that they do not need to be replaced throughout their service life.
5. The enlarged window is designed to be convenient for users to observe the waste papar removing situation of products; both die cutting paper output and stripping paper output adopt double photoelectric detection for abnormal conditions such as paper falling and loose boards.
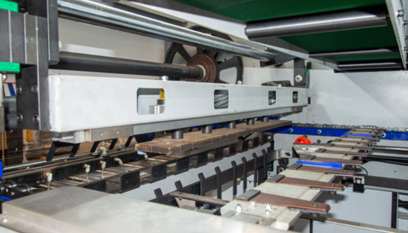
Gripper edge stripping Section of Paper
1.For the front stripping section, pneumatic and compression spring locking devices are adopted. Pneumatic
plate mounting and dismounting are convenient and fast, and the compression spring locking plate is firm
and reliable, so there will be no situation of the plate falling due to low air pressure.
2.The rear gripper - opening also adopts pneumatic and compression spring locking devices; and at the same time, a pneumatic paper - stripping and lifting structure is adopted. When doing full stripping work,the paperstripping part will automatically lift up and will not interfere with the waste paper removing at the front
gripper edge. When the product no need removing the waste paper at the front gripper edge, the paper
stripping part will fall down to directly complete the paper stripping action, without the need for operators to enter the machine for adjustment.
3.The structure of eight gripper bar makes the paper collecting space more spacious, and the operation is
safe and convenient.
4.The pneumatic auxiliary paper collecting structure realizes paper collecting without stopping the machine.
Meanwhile, both the front and rear cylinders can be shut down, which is convenient for collecting large and
small papers.
5.A pneumatic paper supporting mechanism is added to the side paper aligning device, which is convenient
for full waste paper removing die cutting of multi products in one paper, front and rear multi products in one and special shaped cartons.
6. The transmissions of the paper collecting mechanism all adopt cam connecting rod structures without chains, which are easy to maintain, and at the same time are safe and low noise.
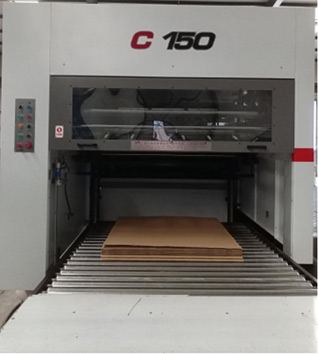
Automatic paper collecting Section
1.For paper collecting and aligning, linear bearings and four bar link structures are adopted. The structure is
simple and the collect papers are neatly.
2. There are an automatic paper stack lifting platform and a counting function to accurately count the number of papers.
3. It can collecting papers without stopping the machine, ensuring the continuous operation of the whole
machine.
4.It has built in functions of counting stack and whole stack paper collecting. For counting stack, all
stainless steel idler rollers are densely arranged without belts, so there is no need to regularly tighten the
belts. Paper can be collecting quickly and conveniently, and high and low position interchange can be
achieved to ensure no scratching or streaking during printing.
5. There is an automatic conversion between non-stop counting paper and whole stack paper collecting .
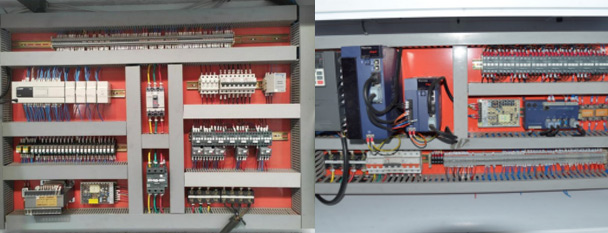
Electronic Control Department
1.The touch screen has real - time communication monitoring, which is stable and convenient for maintenance.
2. With a double electrical box design, the feeder circuit and the main machine circuit are independently
designed to avoid interference problems between low voltage.
2.The fault menu has a memory function, which is convenient for customers to query and maintain.
4. Safety protection devices and warning devices ensure the safety of man and machine.
5. The main motor adopts a high protection level motor and an imported frequency converter, with large
torque and low power consumption.